Industrial Grade SiC: The Workhorse Material
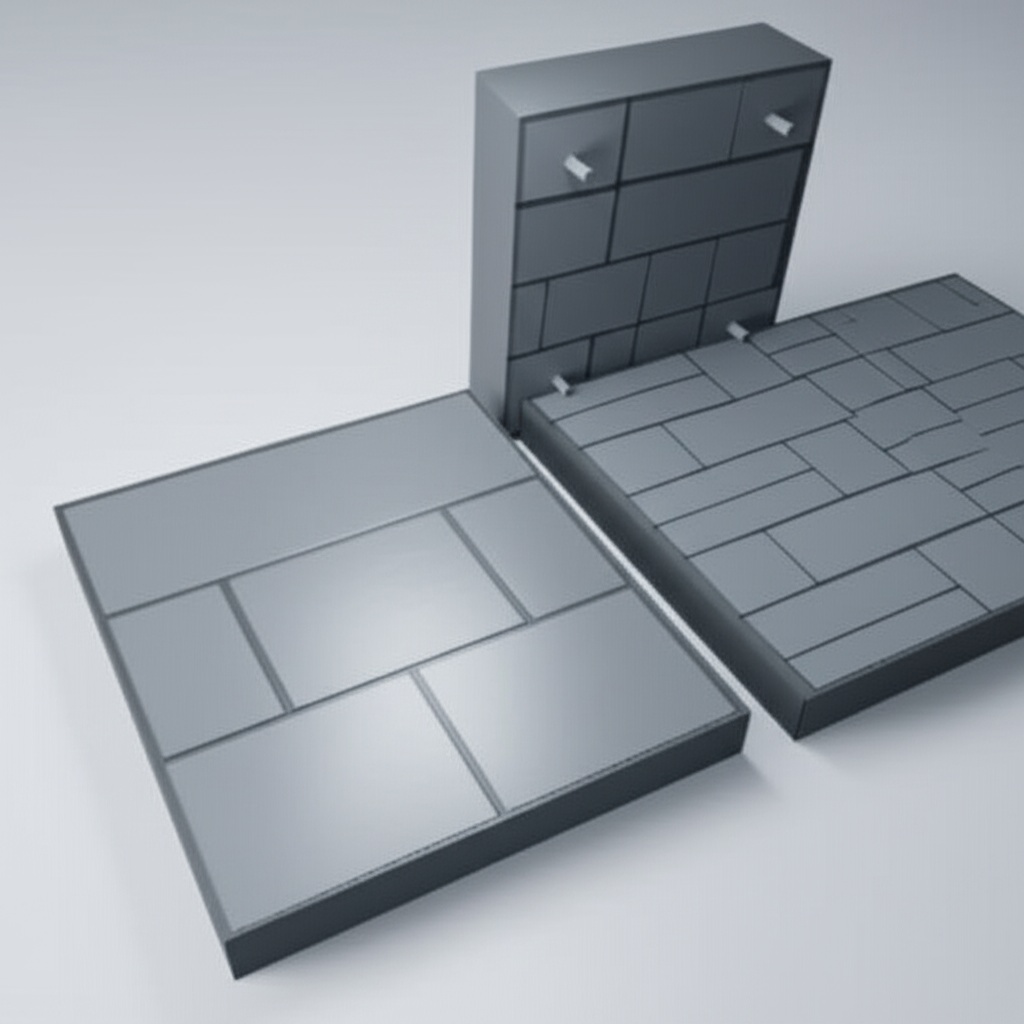
Share
Industrial Grade SiC: The Workhorse Material
In the relentless pursuit of performance, durability, and efficiency across diverse industries, materials science stands as a critical enabler. Among the pantheon of advanced materials, industrial-grade silicon carbide (SiC) has emerged as a true workhorse, consistently delivering exceptional properties that defy the limitations of conventional materials. From the scorching temperatures of industrial furnaces to the intricate demands of semiconductor manufacturing, custom SiC products are redefining what’s possible. This blog post delves into the profound impact of SiC, its myriad applications, and why it’s the material of choice for engineers, procurement managers, and technical buyers seeking unparalleled reliability and performance in their most demanding industrial applications.
Main Applications of Industrial Grade Silicon Carbide
Industrial grade silicon carbide, with its extraordinary properties, finds critical applications across a vast spectrum of industries. Its ability to withstand extreme conditions makes it indispensable in environments where other materials simply fail.
- Semiconductor Manufacturing: SiC is vital for wafer processing equipment, furnace components, and susceptors due to its thermal stability, purity, and low thermal expansion. It ensures precise temperature control and minimizes contamination, crucial for the production of advanced microchips.
- Automotive Companies: In electric vehicles (EVs) and hybrid electric vehicles (HEVs), SiC power electronics significantly improve efficiency and reduce the size and weight of inverters, onboard chargers, and DC-DC converters, extending range and enhancing performance.
- Aerospace Companies: For high-temperature structural components, thermal management systems, and wear-resistant parts in jet engines and spacecraft, SiC offers superior strength-to-weight ratio and exceptional resistance to oxidation and thermal shock.
- Power Electronics Manufacturers: SiC devices enable higher power density, faster switching speeds, and reduced energy losses in power modules, rectifiers, and converters, leading to more efficient and compact power solutions.
- Renewable Energy Companies: SiC is instrumental in solar inverters, wind turbine power converters, and energy storage systems, boosting efficiency and reliability in renewable energy infrastructure.
- Metallurgical Companies: SiC is used for furnace linings, crucibles, and kiln furniture due to its excellent refractory properties, resistance to chemical attack from molten metals, and high thermal conductivity.
- Defense Contractors: For lightweight armor, missile components, and high-performance optics, SiC’s strength, stiffness, and thermal stability are highly valued.
- Chemical Processing Companies: Its exceptional chemical inertness and corrosion resistance make SiC ideal for heat exchangers, pump components, and valves in harsh chemical environments.
- LED Manufacturers: SiC substrates are used for growing GaN (gallium nitride) epitaxial layers, crucial for high-brightness LEDs, due to its excellent lattice match and thermal conductivity.
- Industrial Equipment Manufacturers: SiC finds use in wear parts, nozzles, bearings, and sealing rings for machinery operating under abrasive, corrosive, or high-temperature conditions.
- Telecommunications Companies: SiC is increasingly being adopted in 5G infrastructure, particularly in base station power amplifiers, for its superior efficiency and thermal management capabilities.
- Oil and Gas Companies: In downhole tools, pumps, and valves, SiC’s extreme wear and corrosion resistance ensures longevity and reliability in challenging drilling and extraction environments.
- Medical Device Manufacturers: SiC components are used in high-precision surgical instruments and analytical equipment where biocompatibility, stiffness, and wear resistance are paramount.
- Rail Transportation Companies: SiC power modules are enhancing the efficiency and performance of traction systems in trains and high-speed rail, reducing energy consumption and maintenance needs.
- Nuclear Energy Companies: SiC composites and components are being explored for their radiation resistance and high-temperature performance in advanced nuclear reactors.
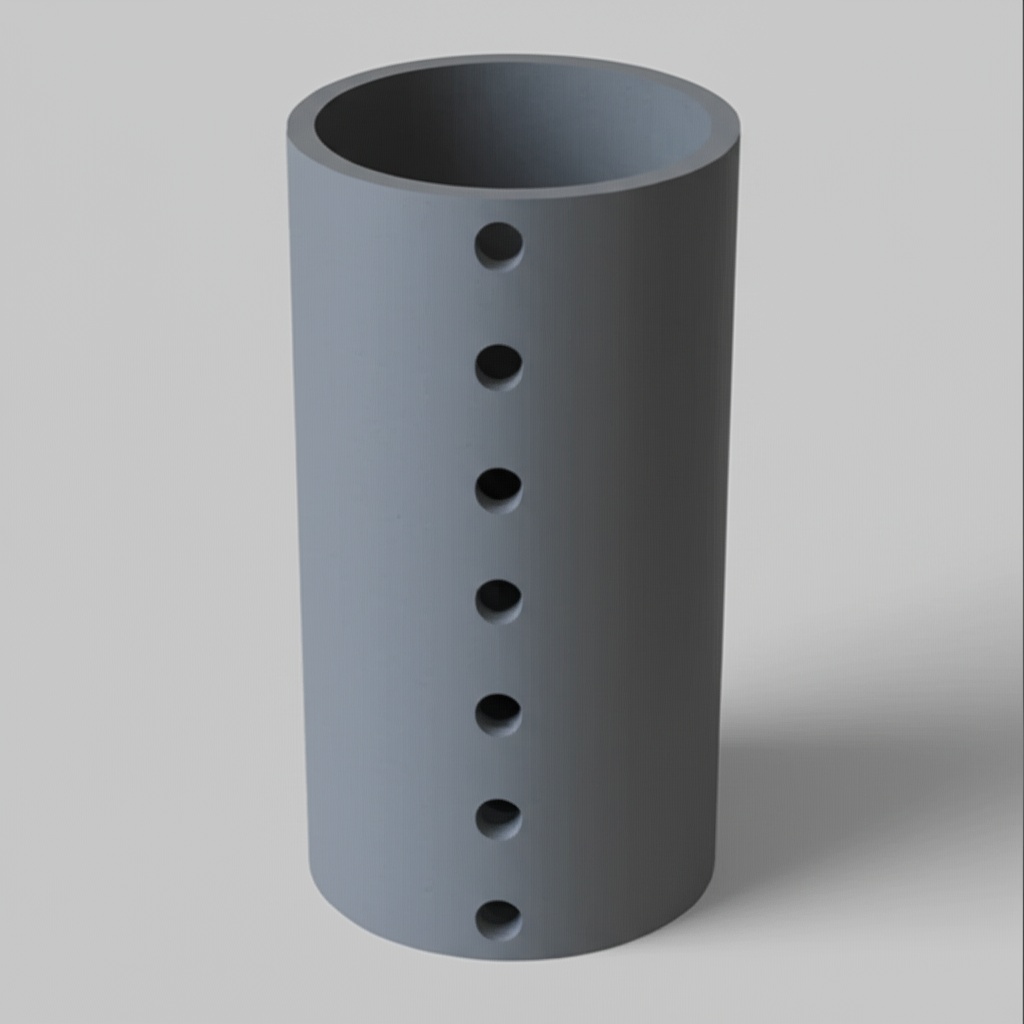
Why Choose Custom Silicon Carbide?
While standard materials may suffice for some applications, the demanding nature of modern industrial processes often necessitates a tailored approach. Custom silicon carbide solutions offer a multitude of benefits that extend beyond off-the-shelf options.
- Thermal Resistance: SiC maintains its strength and structural integrity at extremely high temperatures, far exceeding those of most metals and ceramics.
- Exceptional Wear Resistance: Its inherent hardness makes SiC incredibly resistant to abrasion and erosion, extending the lifespan of components in harsh environments.
- Chemical Inertness: SiC exhibits remarkable resistance to attack from a wide range of corrosive acids, alkalis, and molten metals, making it ideal for chemical processing and metallurgical applications.
- High Thermal Conductivity: This property is crucial for efficient heat dissipation in power electronics and for uniform temperature distribution in thermal processing equipment.
- Low Thermal Expansion: SiC’s low coefficient of thermal expansion minimizes thermal stress and warping, ensuring dimensional stability even under rapid temperature changes.
- Customization for Optimal Performance: Tailored designs allow for optimized performance, precise fit, and integration into complex systems, addressing specific operational challenges.
- Reduced Downtime and Maintenance: The superior durability of custom SiC components leads to fewer failures, reduced maintenance intervals, and ultimately, lower operational costs.
Recommended SiC Grades and Compositions
The performance of silicon carbide can be further optimized by selecting the appropriate grade and composition. Each type offers a unique set of properties suited for specific applications.
SiC Grade/Type | Key Characteristics | Typical Applications |
---|---|---|
Reaction-Bonded SiC (RBSC) | High strength, high thermal conductivity, good wear resistance, complex shapes possible. Contains free silicon. | Kiln furniture, wear parts, heat exchangers, mechanical seals. |
Sintered Alpha SiC (SSiC) | Extremely hard, excellent wear and corrosion resistance, high strength at high temperatures. Pure SiC. | Mechanical seals, bearings, nozzles, pump components, armor. |
Nitride-Bonded SiC (NBSC) | Good thermal shock resistance, moderate strength, good chemical resistance. Lower cost than SSiC. | Kiln furniture, burner nozzles, wear linings. |
Chemical Vapor Deposition SiC (CVD SiC) | Extremely high purity, isotropic properties, theoretical density. Thin coatings and complex geometries. | Semiconductor equipment, optics, mirrors. |
Recrystallized SiC (ReSiC) | Porous structure, excellent thermal shock resistance, high-temperature stability. | Refractory linings, high-temperature insulation. |
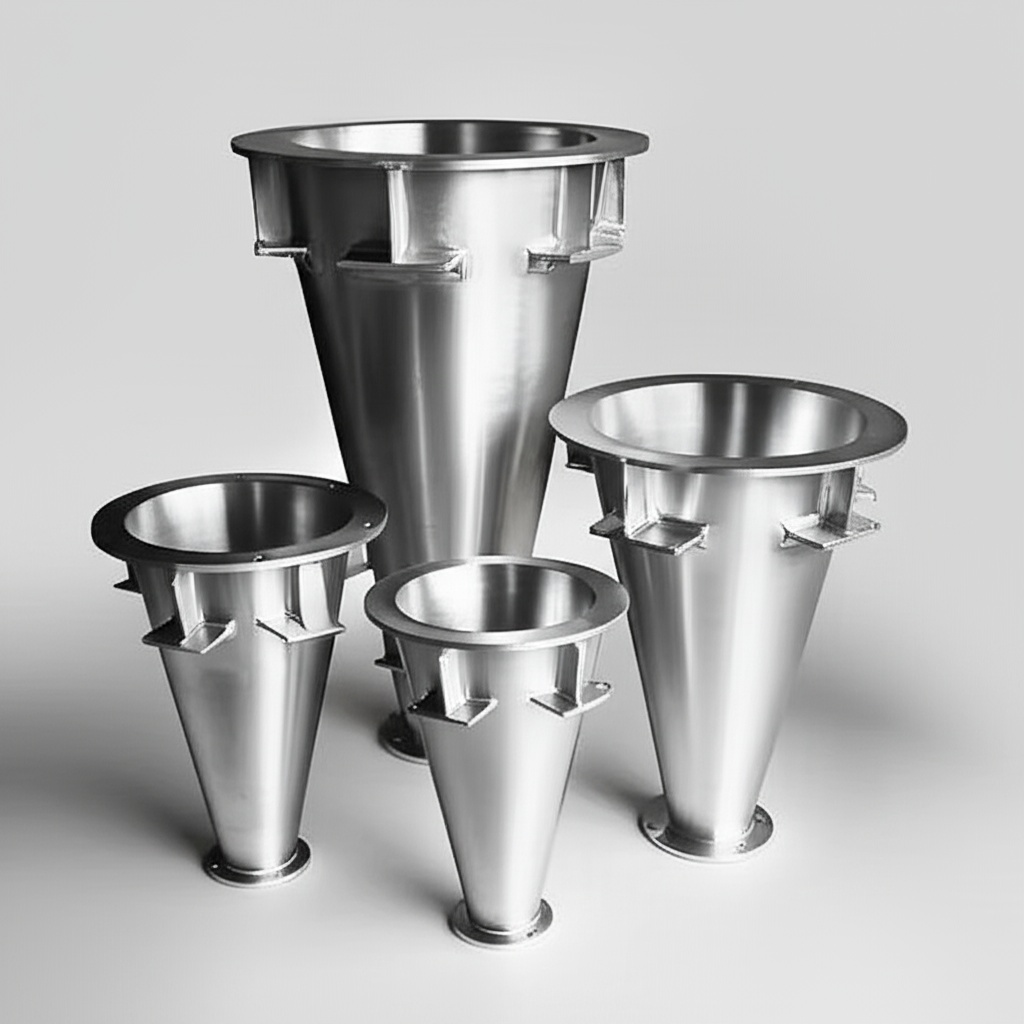
Design Considerations for SiC Products
Designing with silicon carbide requires a nuanced understanding of its material properties to ensure optimal performance and manufacturability. Unlike metals, SiC is a hard, brittle material, and specific design principles must be followed.
- Minimize Stress Concentrations: Avoid sharp corners, abrupt changes in cross-section, and re-entrant angles. Incorporate generous radii and fillets to distribute stress evenly.
- Wall Thickness Uniformity: Maintain consistent wall thicknesses to prevent differential cooling during processing, which can lead to warping or cracking.
- Geometry Limits: While custom SiC products can be highly complex, certain geometries may be challenging or costly to produce. Consult with your custom silicon carbide supplier early in the design phase.
- Mounting and Joining: Consider how the SiC component will be mounted or joined to other materials. Mechanical fastening, adhesive bonding, or brazing methods may require specific design features.
- Thermal Management: Leverage SiC’s high thermal conductivity for applications requiring efficient heat dissipation, and design for appropriate cooling channels or fins if necessary.
- Machining Allowances: Account for post-sintering machining if tight tolerances or intricate features are required.
Tolerance, Surface Finish & Dimensional Accuracy
Achieving precise tolerances and specified surface finishes is critical for the functionality of many industrial SiC components. The manufacturing process dictates the achievable accuracy.
- As-Fired Tolerances: For less critical dimensions, components can be used in their as-fired state, with tolerances typically ranging from $pm0.5%$ to $pm1.5%$ depending on part size and complexity.
- Precision Grinding: For tighter tolerances and smoother surface finishes, diamond grinding is employed. Achievable tolerances can be as low as $pm0.005$ mm for critical dimensions.
- Lapping and Polishing: For optical flatness, extreme surface smoothness, or hermetic sealing applications, lapping and polishing techniques can achieve finishes down to sub-micron levels (e.g., Ra < 0.1 µm).
- Dimensional Stability: SiC’s extremely low coefficient of thermal expansion ensures excellent dimensional stability across a wide temperature range, a significant advantage in high-precision applications.
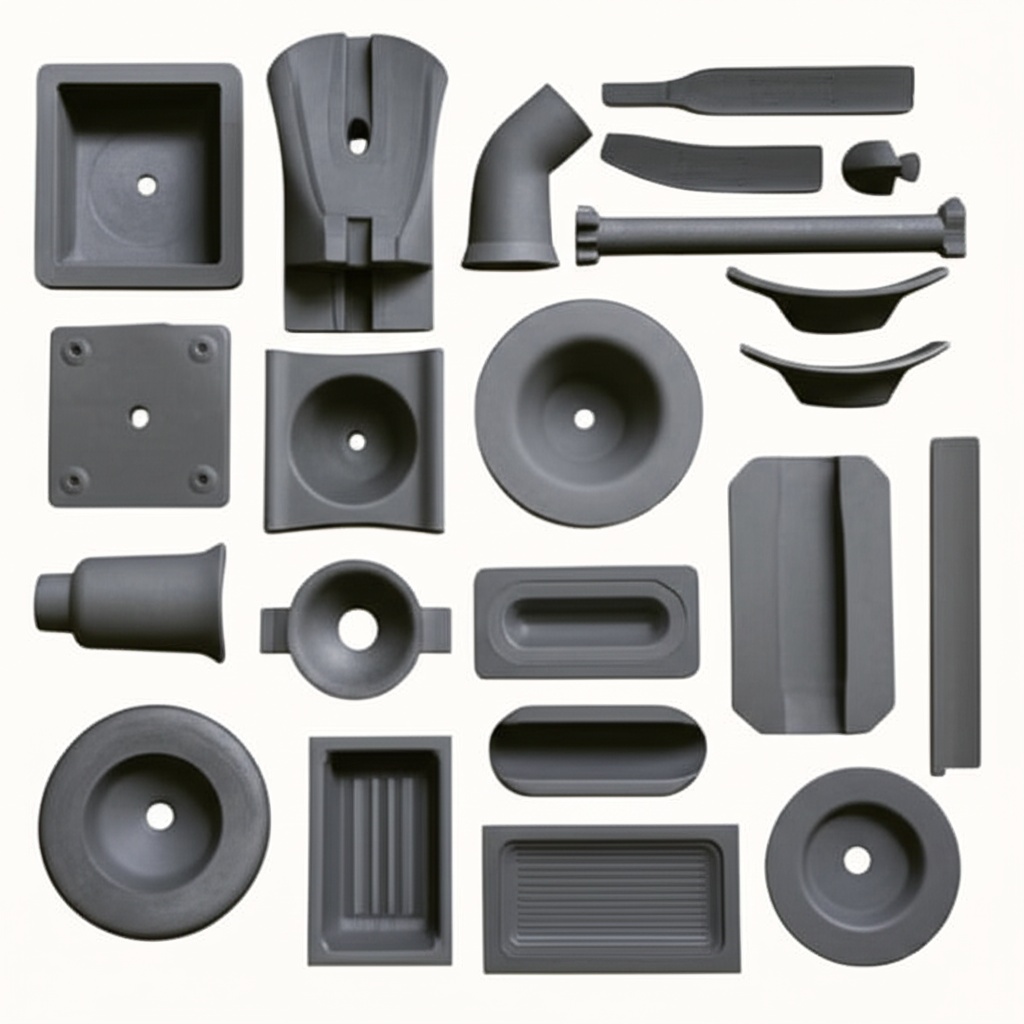
Post-Processing Needs for SiC Components
While SiC is an incredibly durable material, post-processing steps can further enhance its performance, tailor it for specific functions, or meet stringent application requirements.
- Grinding: Precision diamond grinding is routinely used to achieve tight dimensional tolerances, specific geometries, and improved surface finishes after the initial firing process. This is crucial for parts requiring high accuracy.
- Lapping & Polishing: For applications demanding extremely flat or smooth surfaces, such as mechanical seals, optical components, or semiconductor equipment parts, lapping and polishing provide superior surface finishes and flatness.
- Sealing: In certain applications, especially where gas or liquid containment is critical, specialized sealing methods may be applied to SiC components.
- Coating: While SiC is inherently resistant, in some extreme environments, or for specific functional enhancements (e.g., anti-reflective coatings for optics, or even more enhanced corrosion resistance), additional coatings might be applied.
- Laser Marking: For part identification and traceability, laser marking can be used to etch serial numbers or logos onto SiC surfaces.
Common Challenges and How to Overcome Them
Despite its remarkable properties, working with industrial-grade silicon carbide presents unique challenges. Understanding these challenges and how to mitigate them is key to successful application.
- Brittleness: Like most ceramics, SiC is brittle and susceptible to fracture under tensile stress or impact.
- Mitigation: Design components to be primarily under compression. Avoid stress concentrations with generous radii. Handle parts carefully during assembly and operation. Consider SiC composites for enhanced toughness.
- Machining Complexity: SiC’s extreme hardness makes it difficult and costly to machine, especially after sintering.
- Mitigation: Design parts to minimize post-sintering machining. Utilize net-shape or near-net-shape manufacturing processes. Work with suppliers experienced in diamond grinding and other advanced machining techniques for ceramics.
- Thermal Shock Sensitivity: While SiC generally has good thermal shock resistance due to its low thermal expansion and high thermal conductivity, rapid and extreme temperature changes can still pose a risk in some grades.
- Mitigation: Select the appropriate SiC grade for the thermal environment. Design for gradual temperature transitions or incorporate features that help dissipate heat effectively.
- Cost: SiC components can have a higher upfront cost compared to conventional materials.
- Mitigation: Focus on the long-term cost benefits, including extended lifespan, reduced downtime, improved efficiency, and enhanced performance, which often outweigh the initial investment. Optimize designs to reduce material usage and manufacturing complexity.
How to Choose the Right SiC Supplier
Selecting a reputable and capable supplier for your custom silicon carbide products is paramount to project success. A strong partnership ensures quality, reliability, and technical support.
- Technical Expertise: Evaluate the supplier’s understanding of SiC material properties, manufacturing processes, and application challenges. Do they have experienced engineers who can offer design-for-manufacturability insights?
- Material Options: Ensure they offer a wide range of SiC grades (e.g., SSiC, RBSC, NBSC) to match your specific application requirements.
- Manufacturing Capabilities: Verify their capabilities for precision machining, grinding, lapping, and other necessary post-processing steps. Can they handle the complexity and tolerances your design demands?
- Quality Control and Certifications: Look for ISO certifications and robust quality management systems. Request examples of their quality documentation.
- Experience and Track Record: Review their portfolio of past projects and customer testimonials. Do they have experience serving your industry or similar applications? You can check out some of our successful case studies here.
- Collaboration and Communication: A good supplier will be responsive, transparent, and willing to collaborate closely throughout the design and production phases.
It’s important to note that the hub of China’s silicon carbide customizable parts manufacturing is situated in Weifang City of China. This region has become home to over 40 silicon carbide production enterprises of various sizes, collectively accounting for more than 80% of the nation’s total silicon carbide output.
We, Sicarb Tech, have been instrumental in the emergence and ongoing development of this local silicon carbide industry. Since 2015, we have been introducing and implementing advanced silicon carbide production technology, assisting local enterprises in achieving large-scale production and significant technological advancements in product processes. Our deep roots in this manufacturing hub give us a unique advantage.
Sicarb Tech operates under the umbrella of Chinese Academy of Sciences (Weifang) Innovation Park, an entrepreneurial park that collaborates closely with the National Technology Transfer Center of the Chinese Academy of Sciences. This national-level innovation and entrepreneurship service platform integrates innovation, entrepreneurship, technology transfer, venture capital, incubation, acceleration, and scientific and technological services. Capitalizing on the robust scientific, technological capabilities and talent pool of the Chinese Academy of Sciences ,Sicarb Tech serves as a bridge, facilitating the integration and collaboration of crucial elements in the transfer and commercialization of scientific and technological achievements. We have also established a comprehensive service ecosystem that spans the entire spectrum of the technology transfer and transformation process.
This unique position allows us to offer more reliable quality and supply assurance within China. Our domestic top-tier professional team specializes in customized production of silicon carbide products. Under our support, over 312 local enterprises have benefited from our technologies. We possess a wide array of technologies, including material science, process engineering, design, measurement, and evaluation, along with integrated processes from raw materials to finished products. This enables us to meet diverse customization needs with exceptional precision and quality. We can offer you higher-quality, cost-competitive customized silicon carbide components in China. To learn more about our comprehensive customizing support, please visit our website.
Cost Drivers and Lead Time Considerations
The cost and lead time for custom silicon carbide products are influenced by several factors that buyers should be aware of to manage expectations and budget effectively.
- Material Grade: Different SiC grades have varying raw material costs and processing complexities. For example, SSiC is generally more expensive than RBSC due to its higher purity and more intricate sintering process.
- Part Complexity: Intricate geometries, tight tolerances, and features requiring extensive machining will significantly increase manufacturing time and cost. Near-net-shape manufacturing can help reduce this.
- Volume: As with most manufactured goods, higher production volumes typically lead to lower per-unit costs due to economies of scale in material procurement and process setup.
- Surface Finish & Tolerances: Requirements for extremely fine surface finishes or very tight tolerances necessitate additional, time-consuming post-processing steps like lapping and polishing, adding to both cost and lead time.
- Tooling Costs: For new or highly custom designs, initial tooling costs (e.g., for molds or specialized fixtures) can be a significant upfront expense, which is then amortized over the production run.
- Supplier Backlog: The current demand on a supplier’s production capacity can affect lead times. Planning ahead and communicating your project timeline early can help.
If you are looking to build a professional silicon carbide products manufacturing plant in your country, Sicarb Tech can provide you with the technology transfer for professional silicon carbide production, along with a full range of services (turnkey project) including factory design, procurement of specialized equipment, installation and commissioning, and trial production. This enables you to own a professional silicon carbide products manufacturing plant while ensuring a more effective investment, reliable technology transformation, and guaranteed input-output ratio. Discover more about our technology transfer services.
Frequently Asked Questions (FAQ)
Here are some common questions we receive about industrial-grade silicon carbide:
Q1: What are the primary advantages of SiC over traditional ceramics or metals in high-temperature applications?
A1: SiC offers superior high-temperature strength, excellent thermal shock resistance, exceptional wear and corrosion resistance, and high thermal conductivity. These properties allow it to perform reliably in extreme environments where metals melt and traditional ceramics degrade.
Q2: Is silicon carbide electrically conductive?
A2: Pure silicon carbide is a semiconductor. Its electrical conductivity can vary significantly depending on its purity, crystal structure, and doping. In power electronics, SiC is specifically engineered to be a semiconductor for high-efficiency devices, while for structural applications, it is typically considered an insulator.
Q3: How durable is industrial-grade SiC in abrasive environments?
A3: Industrial-grade SiC is one of the hardest and most wear-resistant materials available. Its Mohs hardness is around 9-9.5, making it ideal for components subjected to significant abrasion, such as nozzles, bearings, and wear plates, extending their operational life considerably.
Q4: Can SiC components be repaired or recycled?
A4: Due to its extreme hardness and chemical inertness, traditional repair methods for SiC are challenging. However, some minor damage might be addressed with specialized grinding. Recycling SiC components typically involves grinding them down for use as abrasive grit or in other material compositions, rather than remanufacturing them into new components.
Q5: What is the typical lifespan of a custom SiC component?
A5: The lifespan of a custom SiC component is highly dependent on the specific application, operating conditions (temperature, pressure, abrasive media, chemical exposure), and the design of the component. However, due to SiC’s inherent durability, custom SiC parts often boast lifespans significantly longer than those made from conventional materials, leading to substantial long-term cost savings and reduced downtime.
Conclusion
Industrial-grade silicon carbide stands as an indispensable material in the landscape of advanced manufacturing. Its unique combination of extreme hardness, thermal stability, chemical inertness, and high thermal conductivity makes it the material of choice for the most demanding applications across a myriad of industries, from semiconductors and aerospace to power electronics and chemical processing. The ability to customize SiC components ensures that engineers and procurement managers can precisely tailor solutions to their specific operational challenges, optimizing performance and extending component lifespan. Choosing a knowledgeable and experienced supplier like Sicarb Tech, with its deep roots in China’s silicon carbide manufacturing hub and strong ties to the Chinese Academy of Sciences, ensures not only access to high-quality, cost-competitive customized SiC products but also unparalleled technical support and the potential for strategic technology transfer. Embrace the power of industrial-grade SiC to elevate the performance and reliability of your critical systems. Feel free to contact us today to discuss your specific custom silicon carbide needs.

Sicarb Tech
We, Sicarb Tech has been introducing and implementing silicon carbide production technology since the 2015, assisting the local enterprises in achieving large-scale production and technological advancements in product processes. We have been a witness to the emergence and ongoing development of the local silicon carbide industry.
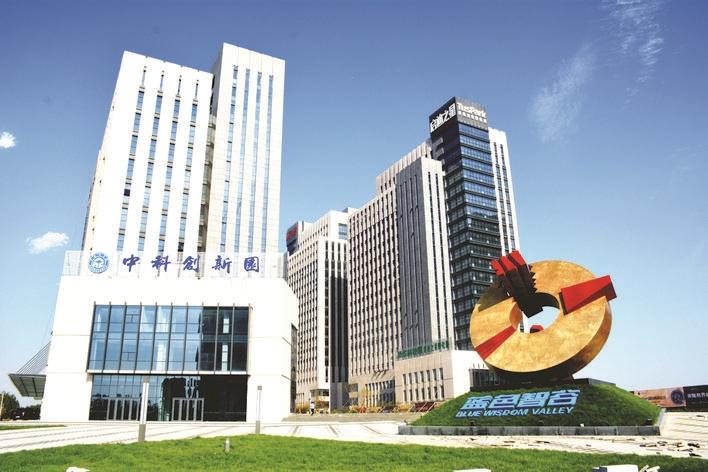