卓越した生産のためのSiC加工をマスターする

シェア
卓越した生産のためのSiC加工をマスターする
炭化ケイ素(SiC)は、今日の最も要求の厳しい産業用途における重要な基幹材料として位置づけられています。その卓越した硬度、高い熱伝導率、優れた耐摩耗性、および化学的慣性により、半導体、自動車、航空宇宙、パワーエレクトロニクス、再生可能エネルギーなどの分野で不可欠な存在となっています。しかし、これらの特性こそが、製造における大きな課題となっています。SiC機械加工をマスターすることは、単なる技術的な偉業ではなく、生産卓越性を達成し、この先進セラミックスの可能性を最大限に引き出すための前提条件です。このブログ記事では、SiC機械加工の複雑さを掘り下げ、技術、課題、およびエンジニア、調達マネージャー、および技術バイヤー向けの最適化された生産への道を探ります。
1. はじめに:炭化ケイ素の機械加工における揺るぎない課題と可能性
炭化ケイ素(SiC)は、ケイ素と炭素の合成結晶化合物です。その顕著な物理的および化学的特性により、過酷な条件下で動作するコンポーネントにとって、非常に求められる材料となっています。灼熱の温度に耐える炉のコンポーネントから、半導体製造装置の精密部品まで、SiCは他の材料が失敗する場所で性能を発揮します。しかし、SiCを非常に価値あるものにしている固有の特性、主にその極度の硬度(ダイヤモンドに次ぐ)と脆性により、従来の機械加工方法では非常に加工が困難になります。SiCの機械加工は、深い材料科学の知識、高度な設備、および綿密に開発されたプロセスを必要とする専門分野です。その可能性は、この困難な材料を、高性能産業におけるイノベーションと効率性を推進する、非常に信頼性の高い精密コンポーネントに変えることにあります。SiCの機械加工を成功させることは、製品寿命の延長、運用効率の向上、および技術的限界を押し上げる能力につながります。
キーワード: 炭化ケイ素の機械加工、先進セラミックス、高性能材料、産業用SiCコンポーネント、SiC製造。

2. なぜ炭化ケイ素は特殊な機械加工の専門知識を必要とするのか
炭化ケイ素の独自の特性は、標準的な機械加工方法からの逸脱を必要とします。これらの特性を理解することは、特殊な専門知識の必要性を理解するための鍵となります。
- 極端な硬度: SiCは通常、モース硬度で9〜9.5(ダイヤモンドは10)を記録し、ヌープ硬度では2500を超えます。これは、従来の切削工具が非常に速く摩耗するか、単に効果がなく、正しく管理しないと高い工具コストと低い生産性につながることを意味します。ダイヤモンドはSiCよりも硬いため、主要な研磨剤として使用されます。
- 脆さ: 硬度が高いにもかかわらず、SiCは脆性材料です。これは、不適切な機械加工力や熱衝撃の下で、チッピング、マイクロクラック、および壊滅的な破壊を起こしやすいことを意味します。機械加工プロセスは、応力集中を最小限に抑えるために慎重に制御する必要があります。
- 高い耐摩耗性: SiCの耐摩耗性は、最終用途での利点がありますが、機械加工工具との相互作用にも適用され、工具の急速な劣化につながります。
- 化学的不活性: SiCの高温での化学的攻撃に対する耐性は、多くの用途で有利ですが、化学的補助機械加工プロセスの選択肢を制限する可能性があります。
- 熱特性: SiCは優れた熱伝導率を持っていますが、機械加工中の局所的な加熱は依然として熱応力を誘発し、適切な冷却と機械加工パラメータで管理しないと、ひび割れにつながる可能性があります。
これらの要因は、SiCの機械加工が単なる材料除去ではなく、材料の完全性を維持しながら、厳しい寸法公差を達成し、望ましい表面仕上げを生成することであることを意味します。これには、特殊な設備、最適化されたプロセスパラメータ、および硬質材料機械加工のニュアンスに熟練した作業員が必要です。調達マネージャーと技術バイヤーは、経験の浅いベンダーによる低コストの機械加工の試みが、多くの場合、部品の故障、プロジェクトの遅延、そして最終的にはより高い全体的なコストにつながることを認識する必要があります。
キーワード: SiC材料特性、硬質材料機械加工、脆性材料機械加工、ダイヤモンド工具、SiC加工性。
3. SiC機械加工技術のスペクトル:従来型から先進型まで
炭化ケイ素コンポーネントを成形するために、さまざまな機械加工技術が開発または適用されています。方法の選択は、SiCグレード(例:焼結SiC(SSiC)、反応焼結SiC(RBSC)、窒化ケイ素結合SiC(NBSC)、CVD SiC)、部品の複雑さ、必要な公差、表面仕上げ、および生産量などの要因によって異なります。
技術 | 説明 | 代表的なアプリケーション | メリット | 制限事項 |
---|---|---|---|---|
ダイヤモンド研磨 | ダイヤモンド砥石を使用して材料を除去します。SiCの最も一般的な方法。 | 成形、サイジング、平坦/円筒表面の実現。 | 優れた材料除去率、高精度が可能。 | 最適化しないと、表面下の損傷を引き起こす可能性があります。工具の摩耗。 |
ラッピングおよび研磨 | ラッピングプレートまたは研磨パッド上で微細なダイヤモンドスラリーを使用して、非常に滑らかで平坦な表面を実現します。 | 光学部品、半導体ウェーハ、シール面。 | 優れた表面仕上げ(Ra < 1 nmが可能)、高い平坦度。 | 材料除去が遅い。主に仕上げ用。 |
放電加工(EDM) | 電極とワークピース間の一連の急速な電気放電を介して材料を除去し、誘電体液中に浸漬します。導電性SiCグレードまたはSiC複合材料に適用可能。 | 複雑な形状、小さな穴、複雑な機能。 | 複雑な形状を機械加工できます。工具とワークピースの直接接触はありません。 | 研削よりも遅い。導電性SiCのみ。熱的損傷の可能性。 |
レーザービーム加工(LBM) | 集束した高エネルギーレーザービームを使用して、材料を溶融、蒸発、またはアブレーションします。 | 小さな穴の穴あけ、スクライビング、薄いセクションの切断、マイクロ機械加工。 | 非接触プロセス。特定のタスクでの高速性。微細な機能を作成できます。 | 熱影響部(HAZ)。マイクロクラックの可能性。材料の再堆積。 |
超音波加工(USM) | 超音波周波数で振動する工具が、ワークピース表面に対して研磨スラリーを推進し、材料のエロージョンを引き起こします。 | 硬くて脆い材料の機械加工、穴あけ、キャビティの作成。 | 非導電性SiCに適しています。低熱応力。 | 材料除去率が低い。工具の摩耗。 |
研磨水ジェット切断(AWJC) | 研磨粒子と混合された高圧水ジェットが材料を浸食します。 | 厚いセクションの切断、ラフシェーピング。 | HAZなし。複雑な輪郭をカットできます。 | 研削と比較して精度と表面仕上げが低い。カットのテーパー。 |
このスペクトルを理解することで、エンジニアと設計者は、特定のSiCコンポーネントの要件に最適な技術または技術の組み合わせを選択できます。
キーワード: SiC研削、SiCラッピング、EDM SiC、レーザー加工SiC、超音波加工SiC、研磨水ジェットSiC。
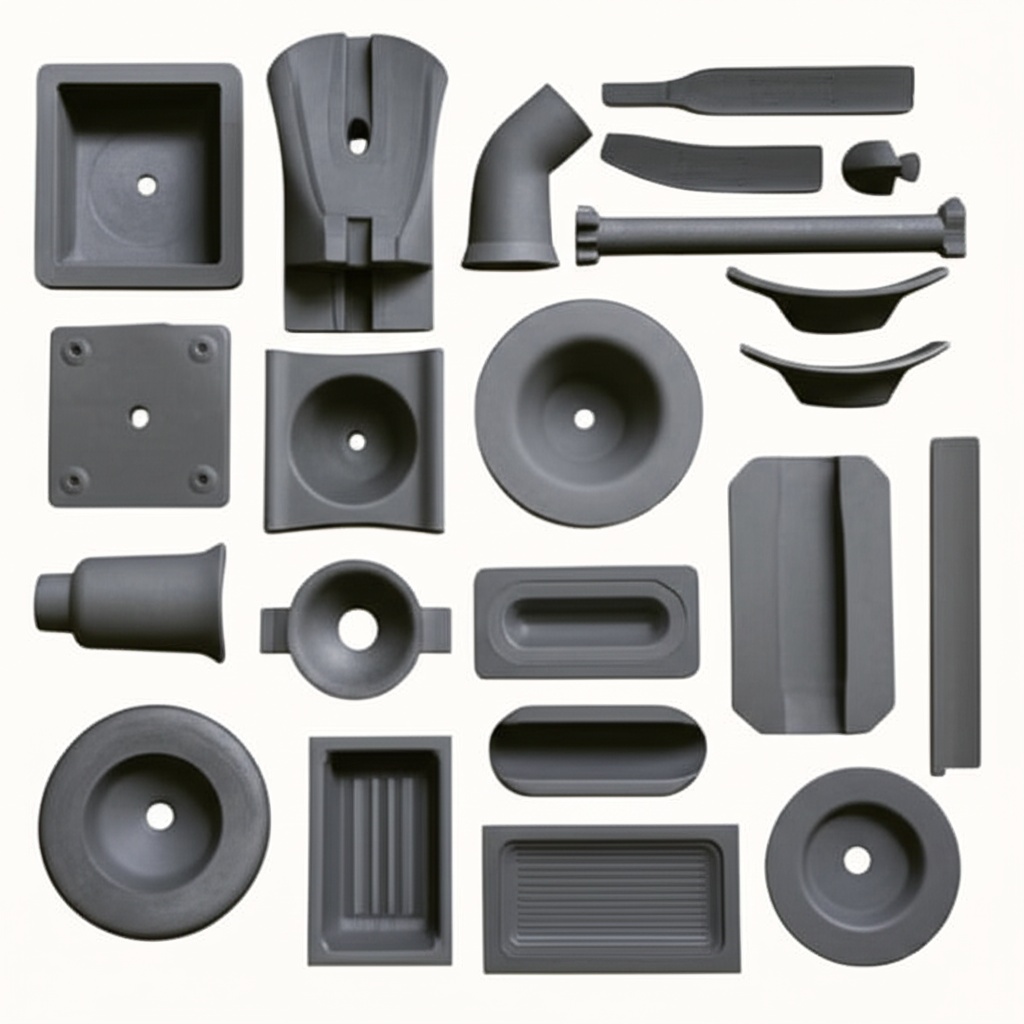
4. 炭化ケイ素の精密研削:SiC機械加工の主力
ダイヤモンド研削は、硬質材料を除去し、正確な寸法を達成する効果があるため、炭化ケイ素の機械加工に最も広く使用されている方法です。SiC研削の成功は、いくつかの重要な要因にかかっています。
- ダイヤモンド研磨剤の選択:
- 種類: 合成ダイヤモンドが一般的に使用されます。金属結合ダイヤモンドホイールは、SiC研削における耐久性と形状保持能力に優れているため、好まれます。レジンボンドホイールは、より細かい仕上げに使用できますが、摩耗率が高くなります。ビトリファイドボンドは、優れた材料除去と形状保持を提供します。
- 砥粒サイズ: 粗いグリット(例:60〜100メッシュ)は、ラフ加工と高い材料除去に使用され、細かいグリット(例:400〜800メッシュ以上)は、より優れた表面品質を実現するために仕上げ加工に使用されます。
- 濃度: ホイール内のダイヤモンド濃度は、切削効率とホイール寿命に影響します。より高い濃度は、より硬いSiCグレードによく使用されます。
- 研削盤の特性: 高い剛性、最小限の振動、および速度と送りの正確な制御が不可欠です。CNC研削盤は、最高の制御と再現性を提供します。
- 動作パラメータ:
- ホイール速度: 最適な速度(通常20〜35 m/s)は、ホイールの種類、SiCグレード、および操作によって異なります。
- 送り速度: チッピングやひび割れの原因となる過度の力を避けるために、慎重に制御する必要があります。SiCでは、より遅い送り速度が一般的です。
- 切り込み深さ: 表面下の損傷を最小限に抑えるために、特に仕上げパス中は、一般的に小さな切込み深さが使用されます。
- クーラントの適用: 研削中に発生する熱を放散し、ワークピースへの熱的損傷を防ぎ、スカフを洗い流すには、効果的な冷却が不可欠です。合成クーラントまたは脱イオン水がよく使用されます。
焼結炭化ケイ素(SSiC)、反応焼結炭化ケイ素(RBSC)、化学蒸着(CVD)SiCなど、さまざまなSiCグレードは、硬度、靭性、および内部応力にばらつきを示します。これらのばらつきは、研削パラメータの調整を必要とします。たとえば、遊離ケイ素を含むRBSCは、完全に高密度のSSiCよりもわずかに加工しやすい場合があります。
キーワード: ダイヤモンド研削SiC、SiC研削ホイール、CNC SiC研削、焼結SiC機械加工、反応焼結SiC機械加工、研削パラメータ。
5. 優れた仕上げの実現:SiCコンポーネントのラッピングと研磨
半導体処理装置、光学ミラー、高性能シール面など、非常に滑らかな表面、高い平坦度、および最小限の表面下の損傷を必要とする用途では、ラッピングと研磨は炭化ケイ素にとって不可欠な研削後のステップです。
- ラッピング: このプロセスでは、SiCワークピースとラッピングプレート(多くの場合、鋳鉄または特殊な複合材料でできています)の間に、緩い研磨スラリー(通常は液体キャリアに懸濁されたダイヤモンド粒子)を使用します。ワークピースは、プレート上をランダムまたは制御されたパスで移動します。
- 目的 平坦度、平行度、および表面仕上げ(通常、Ra 0.05〜0.2 µmの範囲)を改善し、以前の研削操作によって誘発された表面下の損傷を除去するため。
- 研磨剤: 3 µmから30 µmの範囲の粒子サイズを持つダイヤモンドスラリーが一般的であり、望ましい除去率と初期表面状態によって異なります。
- 研磨: 研磨は、さらに細かい表面仕上げを実現するためにラッピングに続き、多くの場合、光学品質(Ra < 1 nm)に達します。このプロセスでは、研磨パッド上でより細かいダイヤモンド研磨剤(通常 < 1 µm、ナノメートルスケールまで)を使用します。研磨パッドは、ポリウレタン、フェルト、または特殊な複合材料などのさまざまな材料で作ることができます。
- 目的 鏡面仕上げを実現し、光の散乱を最小限に抑え、残りのマイクロスクラッチまたは表面下の損傷をさらに減らすため。
- 断面イメージングは、直接的で正確な厚さ測定を提供します。 機械研磨が一般的です。化学機械研磨(CMP)もSiCに採用でき、化学作用が機械的除去を支援し、優れた
SiCラッピングと研磨を成功させるための重要な考慮事項には、以下が含まれます。
- 研磨材のサイズと ラッピングから最終研磨へと工程が進むにつれて、より微細なダイヤモンド粒子が使用されます。
- ラッピングプレート/研磨パッドの材質: この選択は、材料除去率と達成可能な仕上がりに影響を与えます。
- スラリー組成と流量: 適切な分布と潤滑が重要です。
- 圧力と速度: これらのパラメータは、新たな欠陥の発生を避けるために、注意深く制御する必要があります。
- 清潔さ: 清潔な環境を維持することが不可欠です。わずかなコンタミナントでも傷の原因となる可能性があります。
SiC部品でナノメートルレベルの表面仕上げとオングストロームレベルの粗さを実現するには、高度な専門知識と特殊な設備が必要であり、高度なセラミック加工プロバイダーの証となっています。
キーワード: SiCラッピング、SiC研磨、表面仕上げSiC、平面度SiC、光学SiC部品、ケミカルメカニカルポリッシング(CMP)SiC。

6. 複雑さへの対応:複雑なSiC設計のための先進機械加工(EDM、レーザー、USM)
研削、ラッピング、研磨はSiC加工の基盤を形成しますが、特定の用途では、これらの従来の技術では達成が困難または不可能な複雑な形状、複雑な幾何形状、または微細なディテールが求められます。高度な加工プロセスは、これらの複雑さに対するソリューションを提供します。
- 放電加工(EDM):
- 原理: EDMは、熱電侵食を使用して材料を除去します。ワークピースは導電性である必要があります。純粋なSiCは半導体ですが、その導電性は効率的なEDMには不十分な場合があります。ただし、遊離シリコンが豊富なRBSCや、導電性相を持つSiC複合材など、特定のグレードのSiCは、EDMを使用して効果的に加工できます。 SSiCもEDM加工できますが、速度は遅くなります。
- アプリケーション 複雑な3Dキャビティ、鋭い内角、小さく深い穴、複雑なパターンを作成します。ワイヤーEDMは、複雑なプロファイルの切断に使用できます。
- 利点がある: 機械的な力がないため、デリケートな部品に適しています。非常に硬い材料を加工する能力。
- 検討する: 比較的遅い材料除去率。加工面に再キャスト層または熱影響部が発生する可能性があり、後処理が必要になる場合があります。
- レーザービーム加工(LBM):
- 原理: 高強度の集束レーザービームがSiC材料を溶融および蒸発またはアブレーションします。さまざまなレーザータイプ(例:Nd:YAG、エキシマ、フェムト秒レーザー)は、さまざまなタスクに適したさまざまな特性を提供します。
- アプリケーション マイクロホールの穴あけ(例:燃料インジェクター、冷却チャネル)、ウェーハのスクライビング、薄いSiC基板の切断、表面テクスチャの作成、マイクロパターニング。
- 利点がある: 非接触プロセス、特定のタスクでの高速処理、非常に微細な形状を作成する能力。フェムト秒レーザーは、熱損傷を最小限に抑えます。
- 検討する: 熱影響部(HAZ)とマイクロクラックは、注意深く制御しないと、一部のレーザータイプで問題になる可能性があります。材料の再堆積が発生する可能性があります。
- 超音波加工(USM)/超音波振動アシスト研削(UVAG):
- 原理(USM): 目的の形状に成形されたツールは、超音波周波数(通常は> 20 kHz)で振動し、研磨粒子(スラリー中)をワークピース表面に押し付け、マイクロチッピングと浸食を引き起こします。
- 原理(UVAG): 従来のグラインディングホイールまたはツールに超音波振動を重ね合わせます。これにより、切削力が低減され、表面仕上げが向上し、材料除去率が向上する可能性があります。
- アプリケーション 丸い穴または形状の穴の穴あけ、SiCなどの硬くて脆い材料のキャビティのフライス加工。 UVAGは研削性能を向上させます。
- 利点がある: 導電性および非導電性のSiCの両方に効果的です。低熱応力。良好な表面仕上げを生成できます。
- 検討する: 材料除去率は、バルク除去の場合、従来の研削よりも低くなる可能性があります。工具の摩耗が要因です。
高度な加工プロセスの選択は、特定の幾何学的要件、SiCグレードの材料特性、および用途の費用対効果分析に大きく依存します。これらの技術は、多くの場合、従来の技術を補完し、それ以外では加工できない形状に対するソリューションを提供します。
キーワード: EDM炭化ケイ素、レーザー加工炭化ケイ素、超音波加工SiC、マイクロ加工SiC、複雑なSiC部品、高度なSiC製造。
7. 成功のための工具:SiC機械加工用工具の選択と管理
炭化ケイ素の極度の硬度を考慮すると、切削工具の選択と管理は、成功し、費用対効果の高い加工のために最も重要です。ダイヤモンドは、SiC用途のツーリングの紛れもないチャンピオン材料です。
- ダイヤモンドツーリング:
- 種類だ:
- 金属ボンドダイヤモンドツール: ダイヤモンド粒子は、金属マトリックス(例:ブロンズ、鋼、コバルト合金)で焼結されます。これらは堅牢で耐摩耗性があり、グラインディングホイールやコアドリルに適しています。それらは良好な形状保持を提供します。
- レジンボンドダイヤモンドツール: ダイヤモンド粒子は、レジノイドマトリックスに保持されます。これらのツールは、より柔らかい切削作用を提供し、より優れた表面仕上げを生成できますが、金属ボンドよりも早く摩耗します。細かい研削と研磨によく使用されます。
- ビトリファイドボンドダイヤモンドツール: ダイヤモンド粒子は、ガラス状のマトリックスに結合されています。これらは、材料除去率、耐摩耗性、および形状保持能力のバランスが取れています。それらは、シャープさを維持するためにドレッシングできます。
- 電気メッキダイヤモンドツール: 単層のダイヤモンド粒子が、ニッケルメッキによってツール基板に結合されています。複雑な形状や自由切削作用に適していますが、寿命は限られています。
- 多結晶ダイヤモンド(PCD)ツール: PCDは、焼結ダイヤモンド粒子で構成されており、連続したダイヤモンド切削エッジを作成します。 PCDツールは非常に耐摩耗性があり、SiC、特にRBSCまたは硬度の低いSiCの旋削、フライス加工、穴あけに使用されます。研磨工具と比較して、特定の用途でより長い工具寿命を提供します。
- 主要なツールパラメータ: ダイヤモンドのグリットサイズ、濃度、ボンドタイプ、および工具形状(例:PCDツールのすくい角、逃げ角)は、SiCグレード、加工操作(荒加工、仕上げ)、および目的の結果に基づいて慎重に選択する必要があります。
- 種類だ:
- SiC加工における工具摩耗メカニズム:
- 磨耗: SiC粒子の硬度による主な摩耗メカニズム。
- 摩耗: ダイヤモンドグリット切削エッジの平坦化。
- ボンド浸食: ダイヤモンドグリットを保持するボンド材料が摩耗し、グリットの引き抜きにつながります。
- マイクロフラクチャリング: ダイヤモンドグリットは、高い切削力の下で欠けたり、破損したりする可能性があります。
- 工具寿命を延ばし、コストを管理するための戦略:
- 最適な加工パラメータ: 適切な速度、送り、および切り込み深さを使用して、工具へのストレスを最小限に抑えます。
- 効果的な冷却と潤滑: 熱負荷を軽減し、研磨SiC粒子を洗い流すのに役立ちます。
- 工具ドレッシングとトリミング(グラインディングホイールの場合): 新しいダイヤモンドグリットを定期的に露出し、ホイールの幾何学的精度を維持します。
- 高品質のツーリング: 評判の良いサプライヤーから高品質のダイヤモンドツールに投資すると、初期費用は高くなりますが、多くの場合、より優れた全体的な費用対効果が得られます。
- オペレーターのトレーニング: 音響放出センサーまたは電力監視を使用して、工具の摩耗またはプロセスの不安定性の初期兆候を検出します。
ツーリングは、SiC加工において重要なコスト要素を表しています。したがって、生産の卓越性と競争力のある価格を達成するには、慎重な選択、最適化された使用、および積極的な管理を含む包括的なツーリング戦略が不可欠です。
キーワード: SiC用ダイヤモンドツール、PCDツーリングSiC、SiCグラインディングホイール、工具摩耗SiC、加工ツーリング、SiC加工のコスト。
8. 炭化ケイ素機械加工における主要な課題の克服とコンポーネントの完全性の確保
炭化ケイ素の加工は、適切に対処しないとコンポーネントの完全性を損なう可能性のある課題に満ちています。これらの課題を理解し、効果的な緩和戦略を実装することは、信頼性の高いSiC部品を製造するために不可欠です。
- 脆性と破壊:
- チャレンジだ: SiCの低い破壊靭性により、過度の機械的または熱的ストレス下で、チッピング、エッジ破壊、および壊滅的な亀裂が発生しやすくなります。
- 緩和:
- 低切削力(小さな切り込み深さ、制御された送り速度)を使用します。
- 高剛性の工作機械を使用して振動を最小限に抑えます。
- 工具形状の最適化(例:鋭い切削エッジ、工具の適切な面取り)。
- 熱処理プロセスが関与している場合は、徐々に加熱および冷却します。
- ストレス集中を最小限に抑えるように部品を設計します(例:可能な場合は、鋭い内角ではなく丸みを帯びたコーナー)。
- 表面下損傷(SSD):
- チャレンジだ: 研削およびその他の加工プロセスは、加工された表面の下に、マイクロクラック、残留応力、およびアモルファス化された材料の層を導入する可能性があります。 SSDは、SiCコンポーネントの機械的強度と性能を大幅に低下させる可能性があります。
- 緩和:
- 材料除去には粗いグリットから始め、仕上げにはより細かいグリットに進む多段階研削プロセスを使用してSSDを減らします。
- 最終パスでは、穏やかな加工パラメータ(低送り、低切り込み深さ)を使用します。
- 損傷した層を除去するために、ラッピングと研磨を行います。
- 加工後のアニーリングは、SiCの種類と損傷の程度によって効果は異なりますが、応力を緩和し、軽微な亀裂を修復できる場合があります。
- 表面完全性(粗さと波状):
- チャレンジだ: 目的の表面仕上げ(Ra、Rz)と形状精度(波状、平面度)を達成することは、工具の摩耗と材料の硬度により困難になる可能性があります。
- 緩和:
- 研磨グリットサイズと工具タイプの適切な選択。
- 超平滑な表面を実現するための最適化されたラッピングおよび研磨プロセス。
- 適切にメンテナンスされた高精度機械を使用します。
- グラインディングホイールの定期的なドレッシングとトリミング。
- 工具の摩耗と加工コスト:
- チャレンジだ: 工具の急速な摩耗は、ツーリングコストの増加、工具交換のための機械のダウンタイムの増加、および部品品質の潜在的な不整合につながります。
- 緩和:
- SiC用に最適化された高品質のダイヤモンドツールを使用します。
- 最適な加工パラメータと効果的な冷却を実装します。
- PCDや特殊なボンドシステムなどの高度なツーリングを検討します。
- 工具寿命を予測および管理するためのプロセス監視。
- 寸法および幾何学的精度:
- チャレンジだ: 寸法、プロファイル、および幾何学的形状(例:垂直度、平行度)の厳しい公差を維持することは、材料の特性と工具の摩耗により困難です。
- 緩和:
- 高精度で再現性の高いCNCマシンを利用します。
- 可能であれば、インプロセス測定とフィードバック制御を実装します。
- 加工シーケンスの慎重な計画。
- 厳密に管理された条件下で最終的な加工操作を実行します。
これらの課題に対処するには、材料科学の理解、プロセスエンジニアリング、計測学、および経験豊富な人員を組み合わせた総合的なアプローチが必要です。これにより、加工されたSiCコンポーネントが寸法仕様を満たすだけでなく、意図された高性能用途に必要な機械的完全性を備えていることが保証されます。
キーワード: SiC加工の課題、表面下損傷SiC、SiCコンポーネントの完全性、SiC破壊、寸法精度SiC、SiC加工コストの削減。
9. 機械加工されたSiCコンポーネントの品質保証と計測
炭化ケイ素コンポーネントの重要な用途と、その加工における固有の課題を考慮すると、堅牢な品質保証(QA)および計測フレームワークが不可欠です。加工されたSiC部品が、寸法、表面仕上げ、および完全性に関する厳格な仕様を満たしていることを確認することが最も重要です。
加工されたSiCのQAおよび計測の主な側面には、以下が含まれます。
- 寸法検査:
- ツール: 複雑な3D形状用の座標測定機(CMM)、光学比較器、マイクロメーター、キャリパー、ハイトゲージ(多くの場合、耐摩耗性のためにダイヤモンドまたは超硬チップアンビル付き)。
- 検討する: SiC部品の公差は非常に厳しくなる可能性があります(ミクロンまたはサブミクロン)。測定機器の校正が重要です。
- 表面仕上げ測定:
- ツール: スタイラスプロファイラー(例:Talysurf)を使用して、Ra(平均粗さ)、Rz(平均最大高さ)、Rq(二乗平均平方根粗さ)などの表面粗さパラメータを測定します。超研磨された表面のナノメートルスケールの粗さに対する原子間力顕微鏡(AFM)。非接触光学プロファイラー(例:白色光干渉計)。
- 検討する: 表面仕上げ測定ツールの種類は、必要な解像度と表面の性質(例:平坦、湾曲、マイクロフィーチャ)によって異なります。
- 形状および幾何公差の検証:
- パラメータ: 平坦度、平行度、垂直度、真円度、円筒度、同心度。
- ツール: CMM、特殊な形状テスター(例:真円度テスター)、光学表面の平面度評価用の干渉計。
- 表面下損傷(SSD)評価:
- 断面イメージングは、直接的で正確な厚さ測定を提供します。 直接測定は複雑ですが、サンプル部品の間接的な方法と破壊試験を使用できます。これらには以下が含まれます。
- 断面顕微鏡検査: 加工された部品の断面を研磨し、顕微鏡(光学またはSEM)で調べてマイクロクラックを視覚化します。
- 強度試験(例:曲げ試験): 加工されたサンプルと未加工または理想的に準備されたサンプルとの強度を比較します。大幅な強度低下は、重度のSSDを示す可能性があります。
- X線回折(XRD): 表面付近の相変態または残留応力を検出できます。
- 断面イメージングは、直接的で正確な厚さ測定を提供します。 直接測定は複雑ですが、サンプル部品の間接的な方法と破壊試験を使用できます。これらには以下が含まれます。
- 非破壊検査(NDT):
- 染料浸透検査: 表面破壊クラックを明らかにすることができます。
- 超音波検査(高周波): 内部の欠陥、場合によっては表面下の亀裂を検出できますが、細かいSSDには困難です。
- 音響顕微鏡検査: 表面近くの欠陥の検出に役立ちます。
- プロセス制御とドキュメント化:
- 統計的プロセス制御(SPC)を実装して、加工パラメータを監視および制御します。
- 加工プロセス、工具の使用、および検査結果の詳細な記録を維持して、トレーサビリティを確保します(航空
- ISO 9001のような品質管理システムの遵守。
入荷材料検査から最終工程まで、SiC機械加工ワークフロー全体に統合された、包括的な計測戦略。

CAS new materials
We, CAS new materials, have been introducing and implementing silicon carbide production technology since the 2015, assisting the local enterprises in achieving large-scale production and technological advancements in product processes. We have been a witness to the emergence and ongoing development of the local silicon carbide industry.
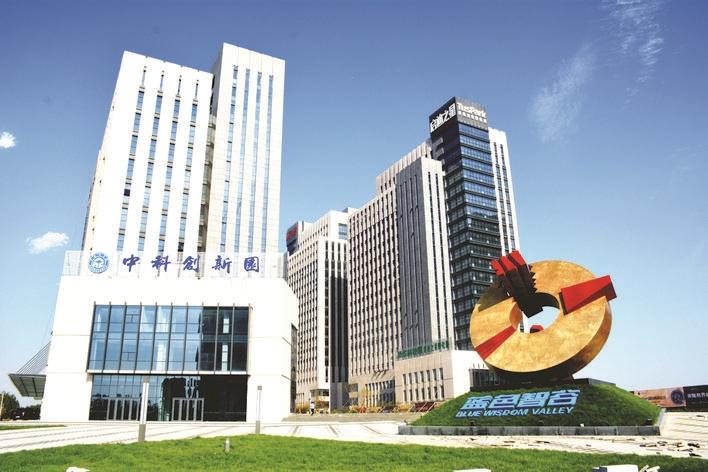