Освоение обработки SiC для повышения качества производства

Поделиться
Освоение обработки SiC для повышения качества производства
Карбид кремния (SiC) является краеугольным материалом в самых требовательных промышленных приложениях. Его исключительная твердость, высокая теплопроводность, превосходная износостойкость и химическая инертность делают его незаменимым в таких отраслях, как полупроводники, автомобилестроение, аэрокосмическая промышленность, силовая электроника и возобновляемые источники энергии. Однако именно эти свойства создают значительные трудности при изготовлении. Освоение технологии обработки SiC - это не просто техническое достижение; это’ необходимое условие для достижения совершенства производства и раскрытия всего потенциала этой передовой керамики. Эта статья в блоге посвящена тонкостям обработки SiC, в ней рассматриваются методы, проблемы и пути к оптимизации производства для инженеров, менеджеров по закупкам и технических покупателей.
1. Введение: Непреодолимые трудности и перспективы обработки карбида кремния
Карбид кремния (SiC) - это синтетическое кристаллическое соединение кремния и углерода. Его замечательные физические и химические свойства делают его востребованным материалом для компонентов, работающих в экстремальных условиях. От компонентов печей, выдерживающих палящие температуры, до прецизионных деталей в оборудовании для производства полупроводников - SiC обеспечивает производительность там, где другие материалы не справляются. Однако присущие SiC характеристики, делающие его столь ценным, - прежде всего его чрезвычайная твердость (уступающая только алмазу) и хрупкость - делают его труднодоступным для обработки обычными методами. Обработка SiC - это специализированная область, требующая глубоких материаловедческих знаний, передового оборудования и тщательно разработанных процессов. Перспективы заключаются в превращении этого сложного материала в высоконадежные, прецизионные компоненты, которые способствуют инновациям и эффективности в высокопроизводительных отраслях промышленности. Успешная обработка SiC позволяет увеличить срок службы изделий, повысить эффективность работы и расширить технологические границы.
Ключевые слова: Обработка карбида кремния, передовая керамика, высокоэффективные материалы, промышленные компоненты SiC, изготовление SiC.

2. Почему карбид кремния требует специализированной обработки
Уникальные свойства карбида кремния требуют отхода от стандартных методов обработки. Понимание этих свойств - ключ к осознанию необходимости специальных знаний:
- Чрезвычайная твердость: SiC обычно имеет твердость 9-9,5 по шкале Мооса (алмаз - 10) и более 2500 Кнуп. Это означает, что обычные режущие инструменты изнашиваются исключительно быстро или просто неэффективны, что приводит к высоким затратам на инструменты и низкой производительности при неправильном управлении. Алмаз, будучи тверже SiC, является основным используемым абразивом.
- Хрупкость: Несмотря на свою твердость, SiC является хрупким материалом. Это означает, что он подвержен сколам, микротрещинам и катастрофическим разрушениям при неадекватных усилиях обработки или тепловом ударе. Процессы обработки должны тщательно контролироваться, чтобы свести к минимуму концентрацию напряжений.
- Высокая износостойкость: Износостойкость SiC’ является преимуществом при использовании в конечных приложениях, однако она также влияет на взаимодействие с обрабатывающими инструментами, что приводит к быстрому разрушению инструмента.
- Химическая инертность: Устойчивость SiC к химическому воздействию при высоких температурах является преимуществом для многих областей применения, но может ограничивать возможности применения процессов обработки с использованием химических веществ.
- Тепловые свойства: Хотя SiC обладает превосходной теплопроводностью, локальный нагрев во время обработки может вызвать термические напряжения, которые могут привести к образованию трещин, если не обеспечить надлежащее охлаждение и параметры обработки.
Эти факторы означают, что обработка SiC - это не просто удаление материала, но и сохранение целостности материала, достижение жестких допусков на размеры и получение требуемой чистоты поверхности. Для этого требуется специализированное оборудование, оптимизированные параметры процесса и персонал, разбирающийся в тонкостях обработки твердых материалов. Менеджеры по закупкам и технические покупатели должны понимать, что попытки недорогой обработки, предпринимаемые неопытными поставщиками, часто приводят к неудачным деталям, задержкам в реализации проектов и, в конечном счете, к увеличению общих затрат.
Ключевые слова: Свойства материала SiC, обработка твердых материалов, обработка хрупких материалов, алмазный инструмент, обрабатываемость SiC.
3. Спектр технологий обработки SiC: От традиционных до передовых
Для придания формы компонентам из карбида кремния были разработаны или адаптированы различные методы обработки. Выбор метода зависит от таких факторов, как марка SiC (например, спеченный SiC (SSiC), SiC с реакционной связью (RBSC), SiC с нитридной связью (NBSC), CVD SiC), сложность детали, требуемые допуски, качество поверхности и объем производства.
Техника | Описание | Типовые применения | Преимущества | Ограничения |
---|---|---|---|---|
Алмазное шлифование | Для удаления материала используются алмазные абразивные круги. Наиболее распространенный метод для SiC. | Придание формы, размеров, получение плоских/цилиндрических поверхностей. | Хорошая скорость съема материала, высокая точность. | При неоптимальном подходе может вызвать подповерхностные повреждения; износ инструмента. |
Притирка и полировка | С помощью тонкой алмазной суспензии на притирочной пластине или полировальном круге можно получить очень гладкие и ровные поверхности. | Оптические компоненты, полупроводниковые пластины, уплотнительные поверхности. | Отличная чистота поверхности (Ra < 1 нм), высокая плоскостность. | Медленный съем материала; в основном для чистовой обработки. |
Электроэрозионная обработка (EDM) | Удаление материала посредством серии быстро повторяющихся электрических разрядов между электродом и заготовкой, погруженной в диэлектрическую жидкость. Применяется для проводящих марок SiC или композитов SiC. | Сложные формы, маленькие отверстия, замысловатые элементы. | Возможность обработки сложных геометрических форм; отсутствие прямого контакта инструмента с заготовкой. | Медленнее, чем шлифование; только для проводящего SiC; возможно термическое повреждение. |
Обработка лазерным лучом (LBM) | Использует сфокусированный высокоэнергетический лазерный луч для расплавления, испарения или абляции материала. | Сверление небольших отверстий, скрайбирование, резка тонких участков, микрообработка. | Бесконтактный процесс; высокая скорость для выполнения конкретных задач; возможность создания тонких деталей. | Зона термического влияния (ЗТВ); возможность образования микротрещин; повторное осаждение материала. |
Ультразвуковая обработка (USM) | Инструмент, вибрирующий на ультразвуковых частотах, подает абразивную суспензию на поверхность заготовки, вызывая эрозию материала. | Обработка твердых и хрупких материалов, сверление отверстий, создание полостей. | Хорошо подходит для непроводящего SiC; низкая термическая нагрузка. | Снижение скорости съема материала; износ инструмента. |
Абразивная гидроабразивная резка (AWJC) | Струя воды под высоким давлением, смешанная с абразивными частицами, разрушает материал. | Резка толстых секций, грубое профилирование. | Отсутствие зоны термического влияния; возможность резки сложных контуров. | Более низкая точность и чистота поверхности по сравнению со шлифованием; конусность срезов. |
Понимание этого спектра позволяет инженерам и конструкторам выбрать наиболее подходящую методику или комбинацию методик для конкретных требований к SiC-компонентам.
Ключевые слова: Шлифовка SiC, притирка SiC, EDM SiC, лазерная обработка SiC, ультразвуковая обработка SiC, абразивная гидроабразивная обработка SiC.
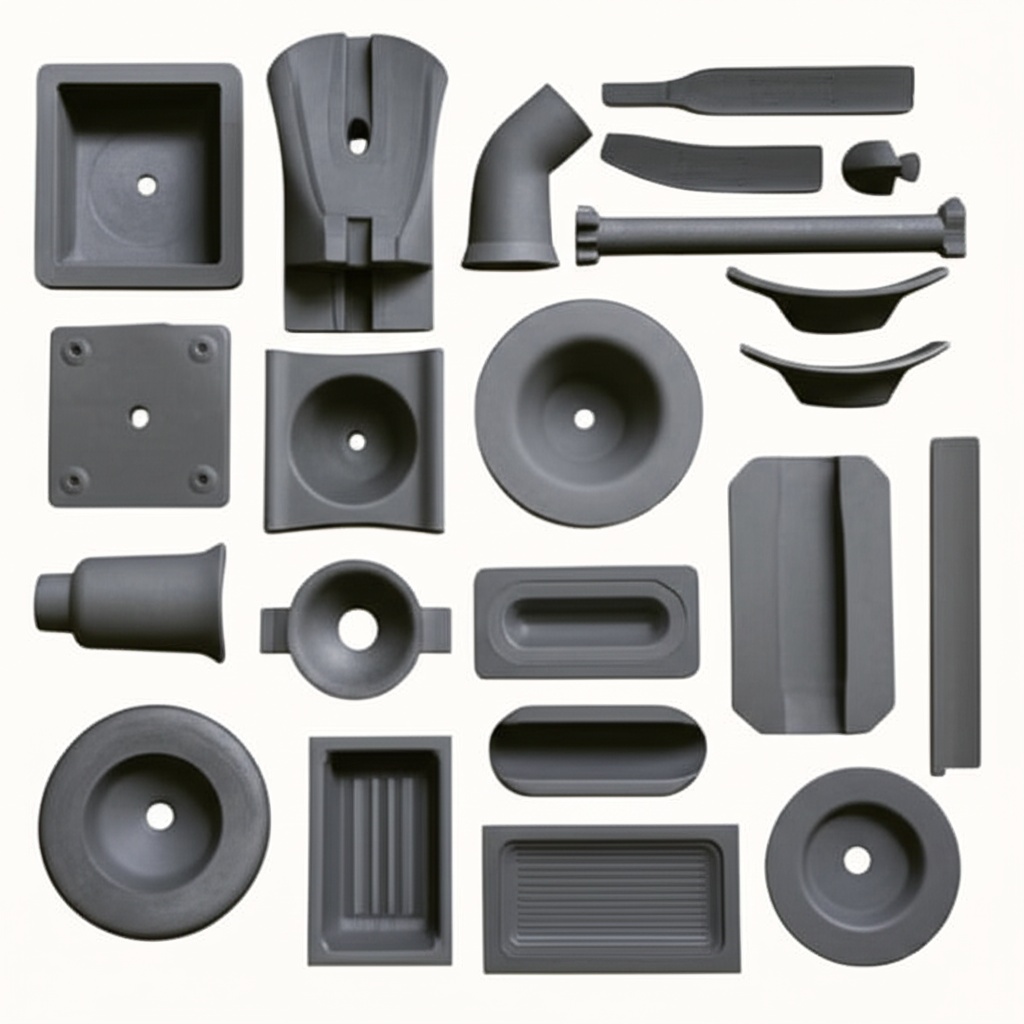
4. Прецизионное шлифование карбида кремния: Рабочая лошадка обработки SiC
Алмазное шлифование является наиболее распространенным методом обработки карбида кремния благодаря его эффективности в удалении твердого материала и достижении точных размеров. Успех шлифования SiC зависит от нескольких критических факторов:
- Выбор алмазного абразива:
- Тип: Обычно используются синтетические алмазы. Алмазные круги на металлической связке предпочтительнее из-за их долговечности и способности удерживать форму при шлифовании SiC. Круги на смоляной связке могут использоваться для более тонкой обработки, но имеют более высокую скорость износа. Стеклокерамические связки обеспечивают хорошее удаление материала и удержание формы.
- Размер зерна: Более грубые зерна (например, 60-100 меш) используются для черновой обработки и снятия большого количества материала, а более мелкие зерна (например, 400-800 меш и мельче) - для чистовой обработки, чтобы добиться лучшего качества поверхности.
- Концентрация: Концентрация алмазов в круге влияет на эффективность резки и срок службы круга. Более высокая концентрация часто используется для более твердых сортов SiC.
- Характеристики шлифовального станка: Высокая жесткость, минимальная вибрация и точный контроль скоростей и подач имеют большое значение. Шлифовальные станки с ЧПУ обеспечивают наилучший контроль и повторяемость.
- Рабочие параметры:
- Скорость вращения колес: Оптимальные скорости (обычно 20-35 м/с) зависят от типа круга, марки SiC и условий эксплуатации.
- Скорость подачи: Необходимо тщательно контролировать, чтобы избежать чрезмерного усилия, которое может привести к сколам или трещинам. Для SiC характерны более низкие скорости подачи.
- Глубина резания: Обычно используется небольшая глубина реза, особенно при чистовой обработке, чтобы свести к минимуму поверхностные повреждения.
- Подача охлаждающей жидкости: Эффективное охлаждение имеет решающее значение для отвода тепла, выделяемого при шлифовании, предотвращения термического повреждения заготовки и удаления стружки. Часто используются синтетические охлаждающие жидкости или деионизированная вода.
Различные марки SiC, такие как спеченный карбид кремния (SSiC), реакционно-связанный карбид кремния (RBSC) и химически осажденный из паровой фазы (CVD) SiC, отличаются по твердости, вязкости и внутренним напряжениям. Эти различия требуют корректировки параметров шлифования. Например, RBSC, содержащий свободный кремний, может обрабатываться немного легче, чем полностью плотный SSiC.
Ключевые слова: Алмазное шлифование SiC, шлифовальные круги SiC, шлифование SiC с ЧПУ, обработка спеченным SiC, обработка SiC на реакционной связке, параметры шлифования.
5. Достижение превосходной отделки: Притирка и полировка компонентов из SiC
В областях применения, требующих исключительно гладких поверхностей, высокой плоскостности и минимальных подповерхностных повреждений, таких как оборудование для обработки полупроводников, оптические зеркала и высокопроизводительные уплотнительные поверхности, притирка и полировка являются обязательными этапами после шлифования карбида кремния.
- Притирка: Этот процесс предполагает использование сыпучей абразивной суспензии (обычно алмазные частицы, взвешенные в жидком носителе) между SiC-заготовкой и притирочной пластиной (часто изготовленной из чугуна или специализированного композита). Заготовка движется по пластине в произвольном или контролируемом направлении.
- Цель: Для улучшения плоскостности, параллельности и чистоты поверхности (обычно в диапазоне Ra от 0,05 до 0,2 мкм), а также для удаления подповерхностных повреждений, вызванных предыдущими операциями шлифования.
- Абразивы: Алмазные суспензии с размером частиц от 3 мкм до 30 мкм являются обычными, в зависимости от желаемой скорости удаления и исходного состояния поверхности.
- Полировка: Полировка следует за притиркой для достижения еще более тонкой отделки поверхности, часто до оптического качества (Ra < 1 нм). В этом процессе используются более мелкие алмазные абразивы (обычно < 1 мкм, вплоть до нанометров) на полировальном коврике, который может быть изготовлен из различных материалов, таких как полиуретан, войлок или специализированные композиты.
- Цель: Для достижения зеркального блеска, минимизации рассеивания света и дальнейшего уменьшения остающихся микроцарапин и подповерхностных повреждений.
- Методы: Обычно используется механическая полировка. Химико-механическая полировка (ХМП) также может применяться для SiC, когда химическое воздействие помогает механическому удалению, что приводит к улучшению целостности поверхности.
Ключевыми моментами для успешной притирки и полировки SiC являются:
- Размер и тип абразива: По мере перехода от притирки к окончательной полировке используются все более мелкие алмазные частицы.
- Материал притирочной пластины/полировальника: Выбор влияет на скорость съема материала и достигаемую чистоту обработки.
- Состав и расход суспензии: Правильное распределение и смазка имеют решающее значение.
- Давление и скорость: Эти параметры необходимо тщательно контролировать, чтобы избежать появления новых дефектов.
- Чистота: Поддержание чистоты очень важно, так как даже небольшие загрязнения могут стать причиной появления царапин.
Достижение нанометрового уровня шероховатости поверхности и ангстремного уровня шероховатости на SiC-компонентах требует значительного опыта и специального оборудования, что делает его отличительной чертой поставщиков передовых технологий обработки керамики.
Ключевые слова: Притирка SiC, полировка SiC, обработка поверхности SiC, плоскостность SiC, оптические компоненты SiC, химико-механическая полировка (CMP) SiC.

6. Навигация по сложности: Передовая обработка для сложных конструкций из SiC (EDM, лазер, USM)
Шлифовка, притирка и полировка составляют основу обработки SiC, однако в некоторых случаях требуются сложные элементы, сложная геометрия или микромасштабные детали, которые трудно или невозможно получить с помощью этих традиционных методов. Передовые процессы обработки предлагают решения для таких сложных задач:
- Электроэрозионная обработка (EDM):
- Принцип: EDM использует термоэлектрическую эрозию для удаления материала. Для этого необходимо, чтобы заготовка была электропроводной. Хотя чистый SiC является полупроводником, его электропроводность может быть недостаточной для эффективного EDM. Однако некоторые сорта SiC, например, некоторые типы RBSC со значительным содержанием свободного кремния или композиты SiC с проводящими фазами, могут эффективно обрабатываться с помощью EDM. SSiC также можно обрабатывать электроэрозионным способом, хотя и с меньшей скоростью.
- Приложения: Создание сложных трехмерных полостей, острых внутренних углов, небольших глубоких отверстий и замысловатых узоров. Проволочная электроэрозионная обработка может использоваться для резки сложных профилей.
- Преимущества: Отсутствие механической силы, что очень удобно для обработки хрупких деталей. Возможность обработки очень твердых материалов.
- Соображения: Относительно низкая скорость удаления материала. Возможность образования на обработанной поверхности слоя повторного литья или зоны термического воздействия, что может потребовать последующей обработки.
- Обработка лазерным лучом (LBM):
- Принцип: Высокоинтенсивный сфокусированный лазерный луч расплавляет и испаряет или аблатирует материал SiC. Различные типы лазеров (например, Nd:YAG, эксимерные, фемтосекундные) обладают различными характеристиками, подходящими для решения разных задач.
- Приложения: Сверление микроотверстий (например, для топливных форсунок, каналов охлаждения), скрайбирование пластин, резка тонких SiC-подложек, создание поверхностных текстур и нанесение микрошаблонов.
- Преимущества: Бесконтактный процесс, высокая скорость обработки для определенных задач, возможность создания очень тонких элементов. Фемтосекундные лазеры минимизируют тепловые повреждения.
- Соображения: Зона термического влияния (ЗТВ) и микротрещины могут быть проблемой при использовании некоторых типов лазеров, если их не контролировать. Может произойти повторное осаждение материала.
- Ультразвуковая обработка (USM) / Ультразвуковое виброшлифование (UVAG):
- Принцип (USM): Инструмент, которому придается нужная форма, вибрирует на ультразвуковых частотах (обычно >20 кГц) и гонит абразивные частицы (в суспензии) к поверхности заготовки, вызывая микросколы и эрозию.
- Принцип (UVAG): Накладывает ультразвуковые колебания на обычный шлифовальный круг или инструмент. Это снижает силы резания, улучшает качество поверхности и повышает скорость съема материала.
- Приложения: Сверление круглых или фигурных отверстий, фрезерование полостей в твердых и хрупких материалах, таких как SiC. UVAG повышает производительность шлифования.
- Преимущества: Эффективен как для проводящего, так и для непроводящего SiC. Низкий уровень термического напряжения. Обеспечивает хорошее качество обработки поверхности.
- Соображения: Скорость съема материала может быть ниже, чем при обычном шлифовании для удаления основной массы. Износ инструмента является одним из факторов.
Выбор передового процесса обработки в значительной степени зависит от конкретных геометрических требований, свойств материала марки SiC и анализа затрат и выгод для конкретного применения. Эти технологии часто дополняют традиционные методы, обеспечивая решения для деталей, которые иначе невозможно было бы обработать.
Ключевые слова: Карбид кремния EDM, лазерная обработка карбида кремния, ультразвуковая обработка SiC, микрообработка SiC, сложные детали SiC, передовое производство SiC.
7. Инструментарий для успеха: Выбор и управление инструментами для обработки SiC
Учитывая чрезвычайную твердость карбида кремния, выбор и управление режущим инструментом имеют первостепенное значение для успешной и экономически эффективной обработки. Алмаз - бесспорный лидер среди материалов для изготовления инструментов для обработки SiC.
- Алмазные инструменты:
- Типы:
- Алмазные инструменты Metal Bond: Алмазные частицы спекаются в металлической матрице (например, бронза, сталь, кобальтовые сплавы). Они прочны и износостойки, подходят для шлифовальных кругов и корончатых сверл. Они хорошо держат форму.
- Алмазные инструменты на смоляной связке: Алмазные частицы находятся в матрице из смолы. Эти инструменты обеспечивают более мягкое режущее действие и позволяют получить более качественную поверхность, но изнашиваются быстрее, чем металлические связки. Часто используются для тонкой шлифовки и полировки.
- Алмазные инструменты со стеклокерамической связкой: Алмазные частицы соединены в стеклоподобную матрицу. Они обеспечивают хороший баланс между скоростью удаления материала, износостойкостью и способностью удерживать форму. Для поддержания остроты их можно подшлифовать.
- Гальванические алмазные инструменты: Один слой алмазных частиц прикреплен к подложке инструмента с помощью никелирования. Хорошо подходят для сложных форм и свободного резания, но имеют ограниченный срок службы.
- Инструменты из поликристаллического алмаза (PCD): PCD состоит из спеченных алмазных частиц, создающих непрерывную алмазную режущую кромку. Инструменты PCD обладают высокой износостойкостью и используются для точения, фрезерования и сверления SiC, особенно RBSC или SiC с низкой твердостью. Они обеспечивают более длительный срок службы инструмента в конкретных условиях применения по сравнению с абразивными инструментами.
- Основные параметры инструмента: Размер алмазной крошки, ее концентрация, тип связки и геометрия инструмента (например, угол ракеля, угол зазора для инструментов PCD) должны быть тщательно подобраны в зависимости от марки SiC, операции обработки (черновая, чистовая) и желаемого результата.
- Типы:
- Механизмы износа инструмента при обработке SiC:
- Абразивный износ: Основной механизм износа обусловлен твердостью частиц SiC.
- Аттриционный износ: Плоская обработка режущих кромок алмазным зерном.
- Эрозия связей: Связующий материал, удерживающий алмазные зерна, изнашивается, что приводит к вырыванию зерен.
- Микроразрыв пласта: Алмазные зерна могут скалываться или ломаться при больших усилиях резания.
- Стратегии продления срока службы инструментов и управления затратами:
- Оптимальные параметры обработки: Использование правильных скоростей, подач и глубин резания для минимизации нагрузки на инструмент.
- Эффективное охлаждение и смазка: Снижает тепловую нагрузку и помогает смыть абразивные частицы SiC.
- Правка и зачистка инструмента (для шлифовальных кругов): Регулярное нанесение свежих алмазных зерен и поддержание геометрической точности круга’.
- Высококачественные инструменты: Инвестиции в алмазные инструменты высшего качества от надежных поставщиков часто дают более высокую общую экономическую эффективность, несмотря на более высокую первоначальную стоимость.
- Мониторинг процесса: Использование датчиков акустической эмиссии или мониторинга мощности для обнаружения ранних признаков износа инструмента или нестабильности процесса.
Инструментарий представляет собой значительный компонент затрат при обработке SiC. Поэтому комплексная стратегия оснастки, включающая тщательный выбор, оптимизацию использования и проактивное управление, имеет решающее значение для достижения высоких производственных показателей и конкурентоспособных цен.
Ключевые слова: Алмазные инструменты для SiC, PCD инструмент SiC, шлифовальные круги SiC, износ инструмента SiC, оснастка для обработки, стоимость обработки SiC.
8. Преодоление основных трудностей при обработке карбида кремния и обеспечение целостности деталей
Обработка карбида кремния сопряжена с трудностями, которые могут нарушить целостность деталей, если их не решить должным образом. Понимание этих проблем и внедрение эффективных стратегий их решения жизненно важно для производства надежных деталей из SiC.
- Хрупкость и излом:
- Вызов: Низкая вязкость разрушения делает SiC чувствительным к сколам, разрушению краев и катастрофическому растрескиванию при чрезмерных механических или термических нагрузках.
- Смягчение последствий:
- Использование низких сил резания (малая глубина резания, контролируемая скорость подачи).
- Использование станков с высокой жесткостью для минимизации вибраций.
- Оптимизация геометрии инструмента (например, острые режущие кромки, соответствующие фаски на инструментах).
- Постепенное нагревание и охлаждение, если речь идет о тепловых процессах.
- Конструирование деталей для минимизации концентрации напряжений (например, скругленные углы вместо острых внутренних углов, где это возможно).
- Подповерхностное повреждение (ПП):
- Вызов: Шлифование и другие процессы механической обработки могут привести к образованию слоя микротрещин, остаточных напряжений и аморфизованного материала под обработанной поверхностью. Твердое твердое тело может значительно ухудшить механическую прочность и эксплуатационные характеристики SiC-компонента.
- Смягчение последствий:
- Использование многоступенчатого процесса шлифования, начиная с грубых зерен для удаления материала и переходя к более мелким зернам для финишной обработки, позволяет снизить твердость диска.
- Использование щадящих параметров обработки (малая подача, малая глубина резания) при завершающих проходах.
- Притирка и полировка для удаления поврежденного слоя.
- Отжиг после обработки иногда может снять напряжения и залечить небольшие трещины, хотя его эффективность зависит от типа SiC и тяжести повреждения.
- Целостность поверхности (шероховатость и волнистость):
- Вызов: Достижение требуемой чистоты поверхности (Ra, Rz) и точности формы (волнистость, плоскостность) может быть затруднено из-за износа инструмента и твердости материала’.
- Смягчение последствий:
- Правильный выбор зернистости абразива и типа инструмента.
- Оптимизированные процессы притирки и полировки для получения сверхгладких поверхностей.
- Использование хорошо обслуживаемого, высокоточного оборудования.
- Регулярная правка и шлифовка шлифовальных кругов.
- Износ инструмента и затраты на обработку:
- Вызов: Быстрый износ инструмента приводит к увеличению затрат на оснастку, простою станка при смене инструмента и потенциальному несоответствию качества деталей.
- Смягчение последствий:
- Использование высококачественных алмазных инструментов, оптимизированных для обработки SiC.
- Внедрение оптимальных параметров обработки и эффективного охлаждения.
- Изучение передовых инструментов, таких как PCD или специализированные системы связки.
- Мониторинг процесса для прогнозирования и управления сроком службы инструмента.
- Точность размеров и геометрии:
- Вызов: Соблюдение жестких допусков на размеры, профили и геометрические характеристики (например, перпендикулярность, параллельность) требует больших усилий из-за свойств материала и износа инструмента.
- Смягчение последствий:
- Использование станков с ЧПУ с высокой точностью и повторяемостью.
- Внедрение измерений в процессе и контроля с обратной связью, где это возможно.
- Тщательное планирование последовательности обработки.
- Выполнение операций окончательной обработки в строго контролируемых условиях.
Решение этих задач требует целостного подхода, сочетающего в себе понимание материаловедения, технологические процессы, метрологию и опытный персонал. Это гарантирует, что обработанные SiC-компоненты будут не только соответствовать размерным спецификациям, но и обладать необходимой механической целостностью для применения в высокопроизводительных приложениях.
Ключевые слова: Проблемы обработки SiC, подповерхностные повреждения SiC, целостность компонентов SiC, разрушение SiC, точность размеров SiC, снижение затрат на обработку SiC.
9. Обеспечение качества и метрология для механической обработки компонентов из SiC
Учитывая критически важные области применения компонентов из карбида кремния и присущие им сложности при обработке, надежная система обеспечения качества (ОК) и метрологии имеет большое значение. Обеспечение соответствия обрабатываемых деталей из SiC строгим спецификациям по размерам, качеству обработки поверхности и целостности имеет первостепенное значение.
Ключевые аспекты контроля качества и метрологии при обработке SiC включают в себя:
- Контроль размеров:
- Инструменты: Координатно-измерительные машины (КИМ) для сложных 3D-геометрий, оптические компараторы, микрометры, штангенциркули, высотомеры (часто с алмазными или твердосплавными наковальнями для повышения износостойкости).
- Соображения: Допуски на детали из SiC могут быть очень жесткими (микроны или субмикроны). Калибровка измерительного оборудования имеет решающее значение.
- Измерение шероховатости поверхности:
- Инструменты: Профилометры со щупом (например, Talysurf) для измерения таких параметров шероховатости поверхности, как Ra (средняя шероховатость), Rz (средняя максимальная высота), Rq (среднеквадратичная шероховатость). Атомно-силовая микроскопия (АСМ) для измерения шероховатости нанометрового масштаба на суперполированных поверхностях. Бесконтактные оптические профилометры (например, интерферометрия белого света).
- Соображения: Тип инструмента для измерения шероховатости поверхности зависит от требуемого разрешения и характера поверхности (например, плоская, криволинейная, с микрорельефом).
- Проверка формы и геометрических допусков:
- Параметры: Плоскостность, параллельность, перпендикулярность, округлость, цилиндричность, концентричность.
- Инструменты: КИМ, специализированные тестеры формы (например, тестеры округлости), интерферометры для оценки плоскостности оптических поверхностей.
- Оценка подповерхностных повреждений (ПП):
- Методы: Хотя прямые измерения сложны, можно использовать косвенные методы и разрушающие испытания на образцах деталей. К ним относятся:
- Микроскопия поперечного сечения: Полировка поперечного сечения обработанной детали и исследование его под микроскопом (оптическим или SEM) для визуализации микротрещин.
- Испытания на прочность (например, на изгиб): Сравнение прочности обработанных образцов с необработанными или идеально подготовленными образцами. Значительное снижение прочности может свидетельствовать о серьезных нарушениях твердости.
- Рентгеновская дифракция (XRD): Может обнаружить фазовые превращения или остаточные напряжения вблизи поверхности.
- Методы: Хотя прямые измерения сложны, можно использовать косвенные методы и разрушающие испытания на образцах деталей. К ним относятся:
- Неразрушающий контроль (НК):
- Проверка с помощью красящего пенетранта: Может выявить трещины на поверхности.
- Ультразвуковой контроль (высокая частота): Может обнаружить внутренние дефекты и иногда подповерхностные трещины, хотя это сложно для тонких твердотельных дисков.
- Акустическая микроскопия: Применяется для обнаружения дефектов вблизи поверхности.
- Контроль процессов и документация:
- Внедрение статистического контроля процессов (SPC) для мониторинга и управления параметрами обработки.
- Ведение подробных записей о процессах обработки, использовании инструментов и результатах проверок для отслеживания (очень важно для аэрокосмической, медицинской и оборонной промышленности).
- Соблюдение систем управления качеством, таких как ISO 9001.
Комплексная стратегия метрологии, интегрированная во все технологические процессы обработки SiC, от входного контроля материала до финишной обработки

CAS new materials
We, CAS new materials, have been introducing and implementing silicon carbide production technology since the 2015, assisting the local enterprises in achieving large-scale production and technological advancements in product processes. We have been a witness to the emergence and ongoing development of the local silicon carbide industry.
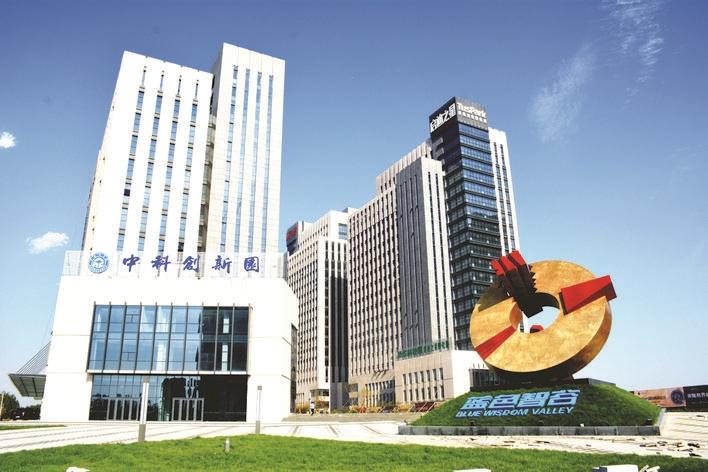